The cracks — or “checks” in the language of the wood industry — aren’t easy to see.
“We had some small check problems with some cherry wood we were drying,” explains Rick Richardson, a lumber purchaser and vice president for Vaughan-Bassett Furniture Company. “We didn’t see any issues until we applied finish to the wood, and the checks would show up.”
For Vaughan-Bassett, the largest manufacturer of bedroom furniture in the United States, such checks — small cracks caused by the separation of wood fibers during the drying process — can have a significant impact on the bottom line.
To help solve the challenge, Vaughan-Bassett consults with College of Natural Resources and Environment Professor Brian Bond, an Extension agent who frequently works with wood products companies in Virginia to provide information and advice about how to improve hardwood drying strategies that turn green wood into wood usable in furniture production.
“We’ve been doing industry-scale lumber drying workshops focused on hardwoods since before my time, and there is still a need,” explained Bond, who teaches in the Department of Sustainable Biomaterials. “This is a hardwood region, and understanding the drying processes we use is incredibly important to the utilization of the resource.”
The cracks are small, but the stakes – for the hardwood industry in the region – could not be greater. The industry has suffered a decade where many hardwood manufacturers have moved overseas for cheaper labor, with the raw materials following. Add the challenges of a COVID pandemic that has caused area mills to delay production, and it is safe to say that the hardwood industry in Appalachia has taken it on the chin recently.
But the challenges of a difficult moment might offer a silver lining: An increased demand for locally sourced products, coupled with new breakthroughs in the treatment and utilization of hardwood, offer promising economic opportunities for the region.
Extension agents like Bond and fellow professor Henry Quesada are in a unique position to help the Appalachian hardwood industry forge a new identity. As scientists and outreach professionals, they play a crucial role in connecting the learning taking place at Virginia Tech with the output that will impact the economy of the Appalachian region.
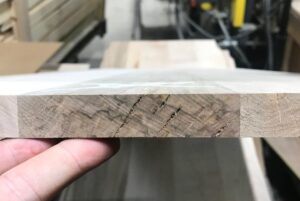
Wood: hard or soft?
Hardwood lumber, sourced from slower-growing, deciduous trees like oak, walnut, and yellow poplar, is renowned for its strength and aesthetic qualities. It is used in furniture construction, flooring, and veneer paneling: If you see wood in your home, you are typically looking at hardwood.
Softwood, on the other hand, like that harvested from spruce, pine, and fir trees, grows faster, costs less, and weighs less. It is in high demand as it is used in the construction and framing of residential homes.
Today, the demand for softwood in the U.S. outstrips the supply, yet upward of 25 percent of American hardwood is exported to factories overseas. That pattern — of having to import softwoods to meet demand while sending high quality hardwood overseas — is one that Quesada would like to change.
One solution? Mass timber. It uses large, solid wood panels for wall, floor, and roof construction.
“Mass timber is a new material that you can use to build buildings higher than five stories,” explained Quesada. “It is a way to utilize hardwoods as a carbon-friendly alternative to concrete or steel.”
To open the door for mass timber to participate in the construction market, Quesada is working with industry associates and lumber producers to conduct three federally funded projects aimed at developing mass timber products, understanding the supply chain challenges to bringing materials to market, and conducting resiliency tests of one version of mass timber — cross-laminated timber — with a manufacturer to demonstrate the efficiency and effectiveness of the product.
“We’ve been working closely with Quesada and Bond on a project that uses poplar in the construction of cross-laminated timber,” explained Tom Inman, president of Appalachian Hardwood Manufacturers Inc., a leading trade association of sawmill distributors in the region. “Our work has shown poplar to have tremendous strength properties, and we’re now at work getting that product approved by national organizations so that architects will specify it and builders will use it.”
There are many benefits to utilizing poplar. It is a fast-growing tree that comes back quickly after harvesting; it can be harvested and processed rapidly; and it thrives in the area, which means that transportation of materials isn’t a significant burden.
“If we can develop a product like mass timber, it has the potential to create jobs and bring back economic development to areas that are currently suffering,” explained Quesada.

To that end, Quesada and Bond have also been working on new ways of treating hardwood to develop alternative uses for the material. In a process called thermal modification, researchers use chambers to heat hardwoods in an oxygen-free environment, causing the wood structures to strengthen.
“The traditional belief is that you can’t use hardwoods for siding because it decays too fast,” he explained. “But we’ve found that thermal modification processes allow us to use hardwoods for flooring applications, decking, and even house siding, where it has a lifespan that matches cedar in durability tests.”
From local connections to global consequences
Finding additional uses for hardwood materials means there are more avenues for the industry to grow. For Extension agents like Quesada and Bond, one specific challenge is getting the message out to professionals who would be interested in using hardwood materials in new ways.
“That’s where the extension part of our job comes in,” said Bond. “A key part of our work is getting out there on the factory floor or in the field with architects and engineers and the people who utilize building materials, so we can explain the benefits of these materials.”
A key avenue for building that rapport is long-standing relationships with industry professionals. Bond has been working with the Flooring Inspectors Educational Guild to provide training on the use of wood flooring materials installed in the home, and potential challenges that may arise with new products.
Bond is also frequently called upon to help solve problems. “Brian is very good at taking the time to answer my calls,” explained Richardson, who has worked at Vaughan-Basset for 43 years. “And if I have any issues at all, he’ll come right up to Galax to help us in any way.”
That kind of access, a keystone in the philosophy of the Virginia Cooperative Extension program, means that Quesada and Bond are able to react quickly to changing demands in the hardwood marketplace, and can even tailor research questions that will have an immediate impact.
“Quesada and Bond stay in close contact with manufacturers in the region,” said Inman. “They know what’s going on in the markets and what’s happening in the industrial, residential, and commercial applications. As a result, they’re able to see if there is a particular angle to a research question that needs to be considered.”
While Bond and Quesada are focused on the area hardwood industry, they stress that increased hardwood utilization has positive global consequences.
“Some of the materials we’re looking to develop new markets for are replacing tropical species that are imported to the U.S. from overseas,” explained Bond. “So we’re using sustainably harvested materials in Virginia that replace materials that are not sustainably harvested elsewhere.”
Using local products to limit the degradation of rainforests and the impacts of transporting materials across the globe is a crucial way for the forestry industry in the region to take a leading role in the green economy of the future. And wood products — from housing materials and siding to the flooring and furniture inside — are passive examples of carbon sequestration.
“Trees can save the world,” said Quesada. “The challenge for the wood industry is finding a unified message that connects their work with that broader message. People understand how trees protect water sources and provide oxygen and habitats for creatures, and we need to draw a clearer connection from those benefits to the benefits of using wood materials. But we have a bright future: We have great forests and great products, and I’m optimistic about the coming years.”
Written by David Fleming